What is Porosity in Welding: Recognizing Its Causes and Enhancing Your Abilities
What is Porosity in Welding: Recognizing Its Causes and Enhancing Your Abilities
Blog Article
The Scientific Research Behind Porosity: A Comprehensive Overview for Welders and Fabricators
Recognizing the elaborate mechanisms behind porosity in welding is critical for welders and makers striving for flawless craftsmanship. As metalworkers dig right into the midsts of this phenomenon, they discover a world regulated by different elements that affect the development of these small gaps within welds. From the composition of the base products to the intricacies of the welding process itself, a plethora of variables conspire to either aggravate or relieve the visibility of porosity. In this comprehensive overview, we will decipher the scientific research behind porosity, discovering its results on weld top quality and introduction progressed methods for its control. Join us on this journey via the microcosm of welding imperfections, where precision satisfies understanding in the pursuit of perfect welds.
Comprehending Porosity in Welding
FIRST SENTENCE:
Exam of porosity in welding reveals crucial insights into the stability and high quality of the weld joint. Porosity, characterized by the existence of tooth cavities or gaps within the weld steel, is a typical worry in welding processes. These voids, if not correctly addressed, can jeopardize the architectural honesty and mechanical homes of the weld, causing potential failures in the completed product.

To find and quantify porosity, non-destructive screening approaches such as ultrasonic testing or X-ray inspection are typically employed. These techniques enable the recognition of inner issues without compromising the stability of the weld. By evaluating the size, form, and circulation of porosity within a weld, welders can make educated decisions to enhance their welding procedures and accomplish sounder weld joints.
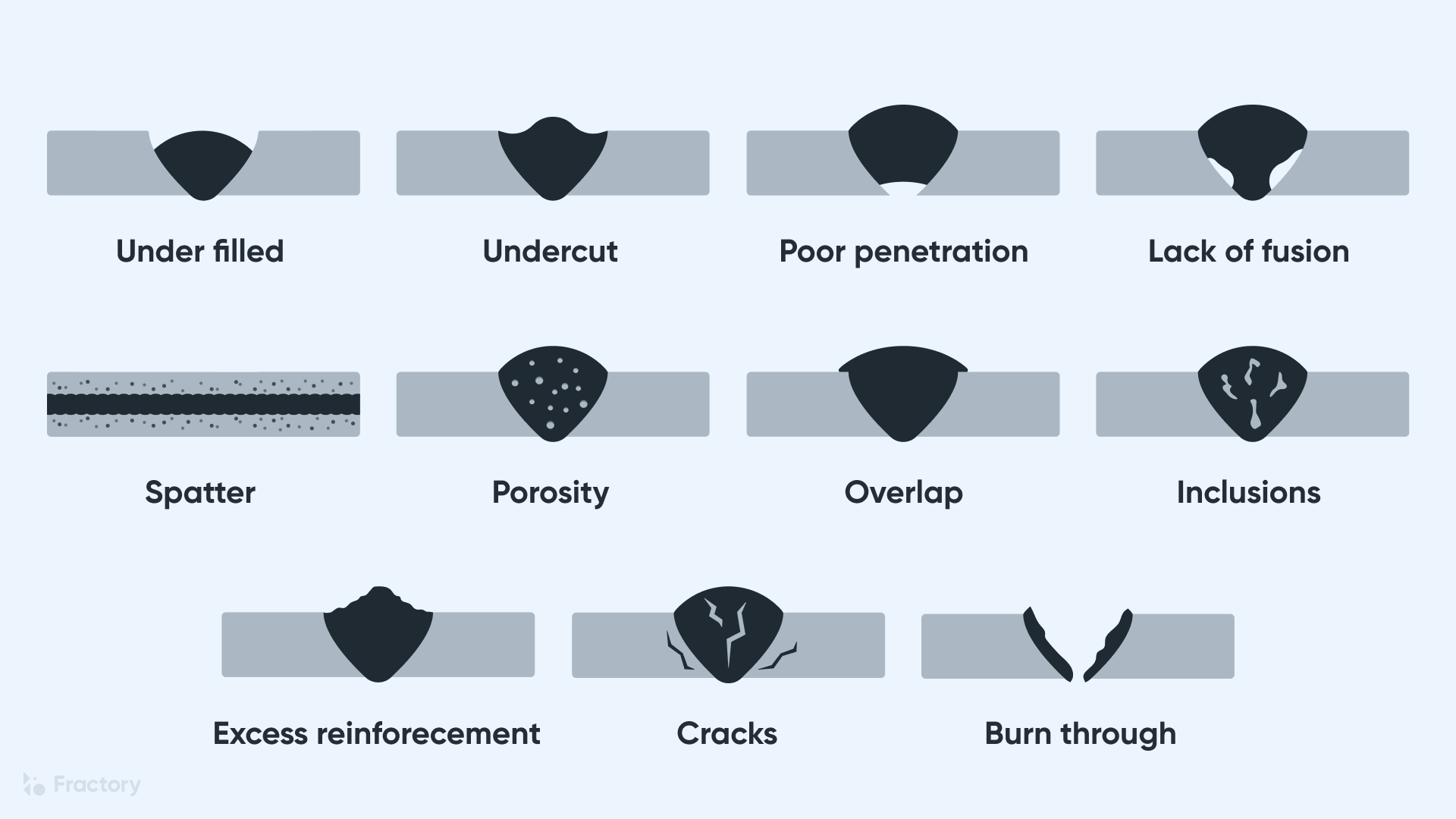
Elements Influencing Porosity Development
The occurrence of porosity in welding is affected by a myriad of factors, varying from gas shielding performance to the details of welding criterion settings. Welding specifications, consisting of voltage, present, take a trip speed, and electrode type, additionally influence porosity formation. The welding technique utilized, such as gas steel arc welding (GMAW) or protected steel arc welding (SMAW), can affect porosity development due to variants in warmth distribution and gas coverage - What is Porosity.
Effects of Porosity on Weld Top Quality
Porosity formation considerably compromises the architectural honesty and mechanical properties of bonded joints. When porosity exists in a weld, it creates spaces or tooth cavities within the product, reducing the overall toughness of the joint. These gaps serve as tension focus factors, making the weld extra vulnerable to breaking and failing under load. The presence of Visit This Link porosity additionally weakens the weld's resistance to deterioration, as the entraped air or gases within the gaps can respond with the surrounding environment, causing degradation in time. Additionally, porosity can prevent the weld's capability to withstand stress or effect, additional endangering the overall high quality and integrity of the welded framework. In vital applications such as aerospace, automobile, or structural buildings, where safety and security and longevity are vital, the destructive impacts of porosity on weld top quality can have extreme repercussions, stressing the importance of reducing porosity with proper welding strategies and procedures.
Techniques to Reduce Porosity
Furthermore, making use of the appropriate welding parameters, such as the appropriate voltage, present, and take a trip speed, is click to find out more critical in protecting against porosity. Preserving a constant arc size and angle during welding likewise aids reduce the probability of porosity.

Using the suitable welding technique, such as back-stepping or employing a weaving motion, can also help disperse warmth equally and minimize the chances of porosity development. By implementing these strategies, welders can effectively lessen porosity and produce high-grade welded joints.
Advanced Solutions for Porosity Control
Executing cutting-edge modern technologies and innovative methods plays a critical duty in attaining premium control over porosity in welding procedures. Additionally, using innovative welding strategies such as pulsed MIG welding or changed environment welding can likewise help mitigate porosity concerns.
An additional advanced solution involves making use click to read of innovative welding equipment. For example, making use of tools with built-in functions like waveform control and sophisticated source of power can improve weld top quality and lower porosity threats. Additionally, the implementation of automated welding systems with accurate control over parameters can substantially lessen porosity flaws.
Additionally, integrating sophisticated monitoring and assessment innovations such as real-time X-ray imaging or automated ultrasonic testing can help in spotting porosity early in the welding process, permitting instant corrective actions. In general, integrating these advanced services can greatly enhance porosity control and boost the total quality of bonded elements.
Conclusion
In final thought, understanding the scientific research behind porosity in welding is essential for welders and makers to create premium welds - What is Porosity. Advanced services for porosity control can further improve the welding process and make sure a strong and trustworthy weld.
Report this page